High-pressure Waterblasting
Eagle Services provides automated high-pressure waterblasting for industrial cleaning needs throughout the Midwest and beyond. We use 10,000 psi water with proprietary high efficiency nozzles to clean foulants from industrial process equipment. 20K, 30K and 40K psi pressures are employed for more tenacious materials.
Eagle Services employs 40K psi water for cutting metals, concrete, wood, and composite materials for applications such as tank entry, plant modification, or surface preparation.
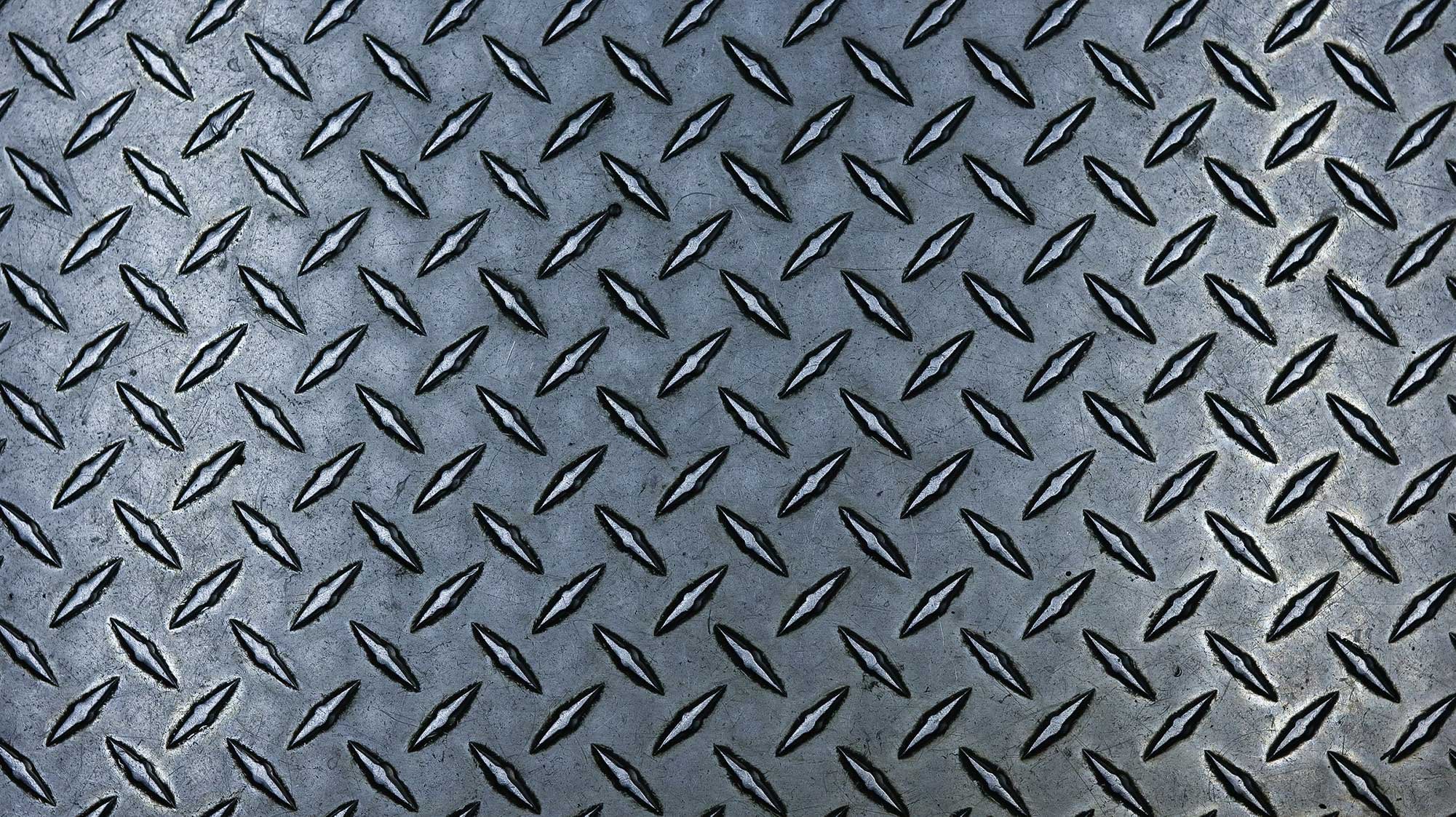
Request a free consultation now
Automated High-Pressure Waterblasting Case Studies
Case Study: Automated High-pressure Waterblasting for a 7000-tube Evaporator
In a cold February, a major corn processor in Lafayette, IN had a major problem. Their waste heat evaporator had gotten completely fouled and was operating well below expectations. After their local contractor could not respond in appropriate time, they called Eagle Services. Eagle Services employed (5) 40k PSI pumps, (3) XY automated tube cleaning system with spinning nozzles, and an around the clock crew to support for 72-hour coverage.
The evaporator had 3 chests with a total of over 7,000 tubes. The job was completed in under 72 hours safely and successfully. The corn processor was able to return to max production rates after firing up ahead of schedule.
Case Study: Automated High-pressure Waterblasting to Clean Paint Booths
Paint booth bottoms had a build up of sludge which was hindering hydro bin air flow.
The booth top was contaminated with dry paint overspray, which posed the threat of falling onto new car paint as production continued. Eagle Services waterblasted the booth top, walls, ceilings, and floor grating removing all paint. The booth bottoms were then hand scraped and vacuumed clean. Eagle Services moved to the paint sludge pits, removing over 400 cubic yards of paint sludge, utilizing 10,000 psi to 40,000 psi waterblasting and vacuuming.
This project was completed safely and on time to allow the start of the production line as scheduled, and the line ran within the quality specifications of the customer.
Case Study: Dry Ice for Food Processing Equipment
A multinational bakery corporation had a contaminated oven with burnt-on carbon which was negatively impacting product integrity.
The oven had to be cleaned and sanitized within an 8 hour down time. Eagle Services employed our dry ice blaster to strip the carbonized material from oven surfaces. Eagle Services then applied a quaternary ammonia sanitizer for the final rinse.
The project was completed in the 8 hour time window, and the product integrity was restored for the owner.
Case Study: Dry Ice Blast to Clean Steam Turbines
A turbine in an ethanol plant needed mineral deposits removed from the blades. Located in a confined space where water would create problems for surrounding electrical components, Eagle Services utilized our dry ice blaster, 200 lbs of CO2 pellets and a 375 CFM air compressor to clean the turbine in 12 hours and put the plant back online and at max production.
Case Study: Automated High-pressure Waterblasting for a 3,000-tube Exchanger at a Chemical Plant
A 3,000 tube exchanger at a chemical plant in Illinois is cleaned successfully.
Hot product passed through the tube side; and cooling water passed across the shell side. The product had set up in the tubes and was not responding to conventional 20,000 psi waterblasting methods, so Eagle Services increased the water pressure to 40,000 psi. This proved to be the most effective, cost efficient cleaning method for the tube side of the exchanger.
Meanwhile, as Eagle Services worked closely with the customer's lab technicians, it was determined there were no significant changes in the chemical properties of the product that could be attributed to the hardening of the product in the tubes. So we turned our attention to the shell side of the exchanger and focused on the exchanger's ability to cool the product.
After obtaining and analyzing scale retrieved from a low point drain, Eagle Services and its customer determined it was necessary to chemically clean the scale from the shell side of the exchanger. Because of the type of scale found and the metallurgy of the exchanger, the solvent of choice was inhibited hydroxyacetic, formic acid in the appropriate ratios.
Since this 48-hour episode, a routine maintenance schedule is followed; and this piece of equipment has not been down for more than 24 hours for cleaning and operates at increased efficiency between cleaning intervals.
Case Study: Automated High-pressure Waterblasting to Clean Rail Cars
A corn processing company had a huge mess on their hands. Several rail cars had been over filled with corn oil and subsequently had spillage all over the outside of their rail cars.
They had also received rail cars from another site where the grain inside had caught fire and was out of service. That company called Eagle Services Corp to solve these problems. Eagle Services utilized their fully automated robotic arm equipped with our high volume 305 hydro blaster to clean the outside of the rail car from a safe distance. After the outside of the rail cars were cleaned, Eagle Services equipped our hydro blaster with a 3D hurricane blaster accessory that broke up the material inside. After material was loose and manageable, Eagle Services Corp used one of their 60, 5000 CFM vacuum trucks to pull material out of the rail car and unloaded to an onsite roll off box. The satisfied customer put their rail cars back into service and carried on with production.
Case Study: Automated High-pressure Waterblasting to Clean Chemical Plant Reactors
During a severe Midwestern snowstorm, the contents of a chemical plant's 20,000 gallon stainless steel reactor hardened inside the vessel.
The hardened contents had to be removed before the reactor could be placed back in service. Due to the snowstorm, all roads, including a major interstate, from Eagle Services' normal service location were closed. Eagle Services' equipment was available from a southern location which was unaffected by the storm; however, the personnel with the proper credentials for the job were unable to drive to the plant. Eagle Services' personnel were taken to a municipal airport, via snowmobiles, and were airlifted by helicopter to the customer's location. At the same time, the equipment was delivered from Eagle Services' southern location.
Eagle Services employed 30,000 psi water and vacuum equipment to remove material from the reactor and worked around the clock to successfully complete the project.
Case Study: Ultra High Pressure Water Cutting for Hydro Demolition of Coke Plant Decanters
An integrated steel mill in Gary, IN shut down their coke plant and needed to conduct a full decontamination and deconstruction of the plant. The coke decanters were still full of coke tar and other hazardous and flammable material. Seeing as the material had become hard over time and there were no accessible manways, the mill was left with a big problem on their hands.
Eagle Services employed a 40,000 PSI hydro blaster with a spark proof garnet injection system to perform “cold cuts” into the tank. Eagle then used large bobcats to drive into the tank to remove the material as well as air movers to suck out residual material. The mill was back on schedule to demolish the plant in their projected time.
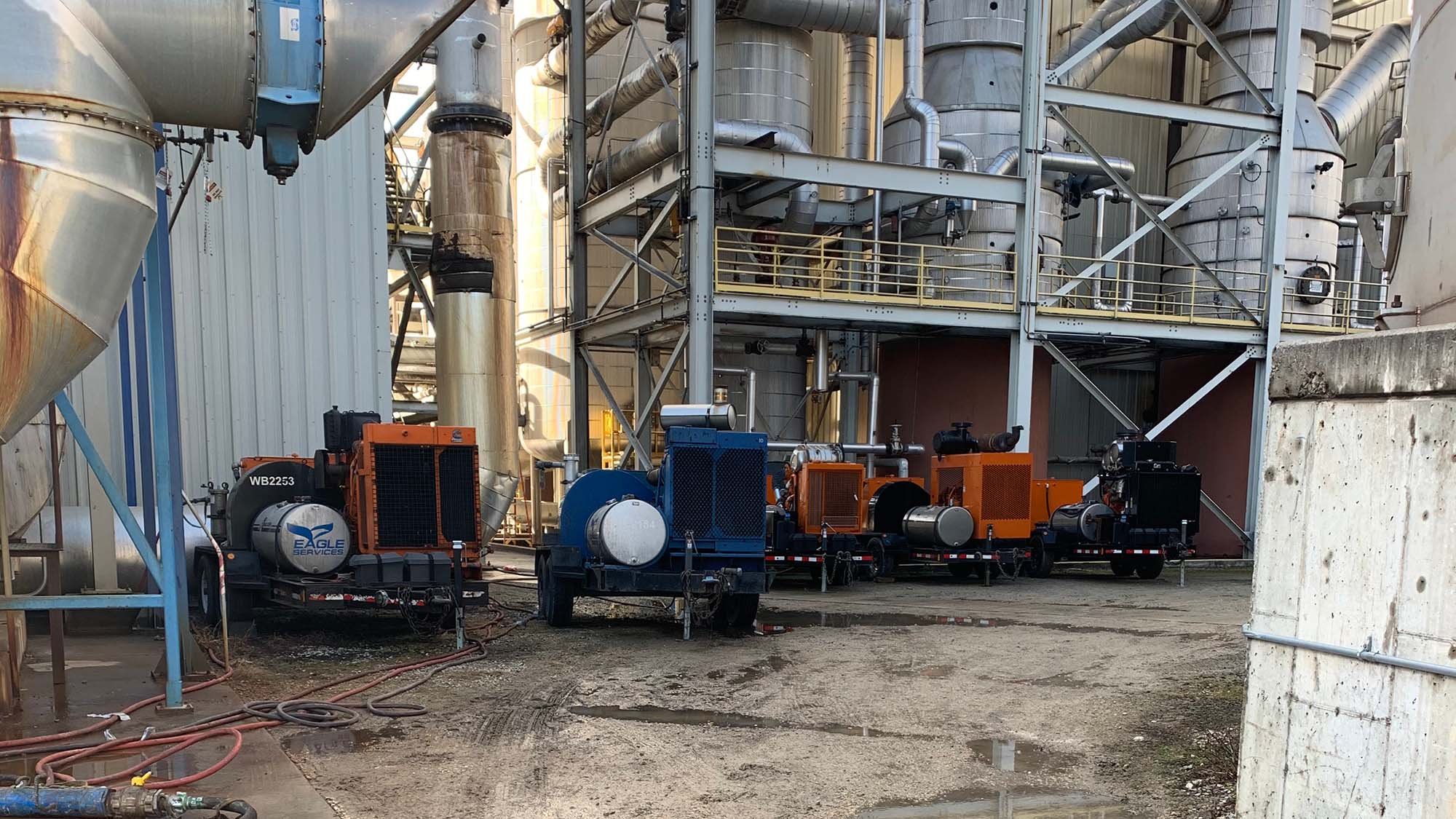