Chemical Recirculation & Chemical Cleaning
Eagle Services provides chemical recirculation and industrial chemical cleaning throughout the Midwest and beyond. We utilize specialized equipment, proprietary chemical blends, and proprietary methodologies to recirculate cleaning compounds through process equipment such as lube oil equipment, food process equipment, oxygen lines, and hydraulic systems for maintenance and pre-operational cleaning.
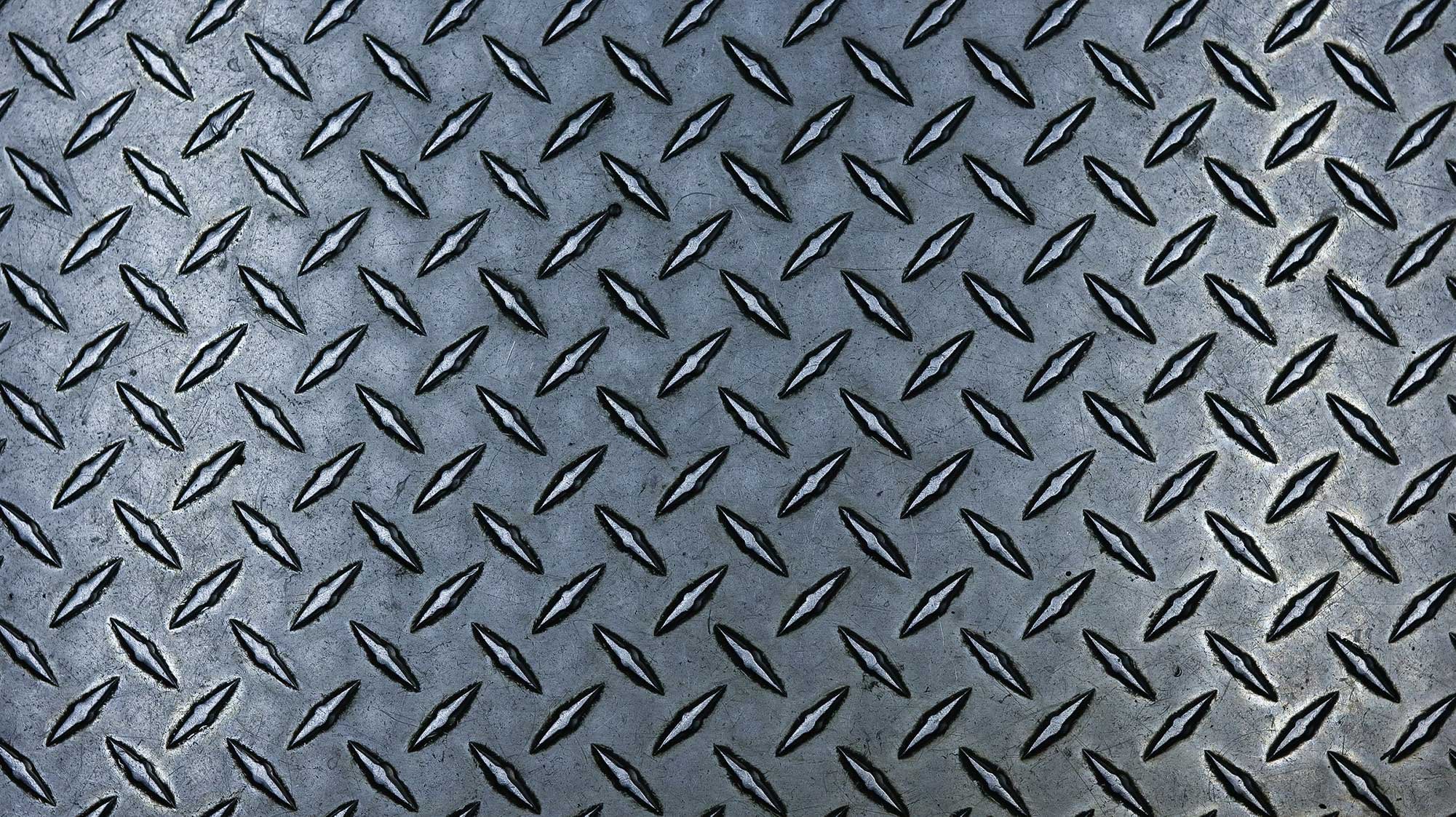
Request a free consultation now
Case Studies
Case Study: Chemical Recirculation to Remove Iron Oxides & Hard Water Deposits
A steel mill needed to remove iron oxide and water hardness deposits from the water jackets on a blast furnace.
Eagle Services was contracted to chemically clean two water jackets on the steel mill’s blast furnace which had become fouled with iron oxides and water hardness deposits. Due to the number of inlets and outlets, pre-job planning to achieve proper flow patterns and velocities was crucial.
Through pre-job planning and scale analysis, Eagle Services came up with a process and procedure to execute the project safely and efficiently using a mixture of wetting agents and organic acids to remove the scale. Once the project started, Eagle Services executed reverse flows every half-hour and monitored the temperature at all ports with a heat gun to ensure that all loops were circulating evenly. We used an explosion-proof, waterproof rheostat control to adjust flow rates and pressures on its self-contained pumping unit as needed to achieve proper flow rates. Eagle Services then used analytical testing to determine when the systems were free of fouling.
Because of the efficiency of Eagle Services’ system, this project was completed more quickly than originally estimated. The client was pleased with Eagle Services' professionalism and the timely completion of the project.
Case Study: Preoperative Cleaning of Process Piping
An oxygen line with down legs in Michigan required preoperative cleaning.
In many cases, cleaning a process pipe or drain can be paralleled to cleaning tubes in an exchanger, and 10,000 psi water can be used. But in some cases, waterblasting is not possible. This was the case with a 1350' line that was newly installed for oxygen use.
Although the line had very few bends, the need to clean its ten down legs made it impossible to "pig" it clean. After confirming the line had room for expansion and all the pipe hangers could be loosened, the cleaning method of choice was Vapor Phasing. Recirculation would have been difficult because the pipe ran 1350' in one direction with no lines available to return a solution or vapor.
After fabricating a steam and chemical injection spool piece for one end and a cold water quench pipe for the other, Eagle Services put 300 pound steam to the line. Once the entire line was hot, the crew followed Eagle Services' procedure for new oxygen service line cleaning.
The first stage was to degrease with caustic, soda ash, SMS, TSP and surfactant in the appropriate ratios. Stage two included an ammoniated citric at the proper pH and concentration. The final stage called for adjusting the pH with ammonia and then adding the proper amount of sodium nitrate to passivate.
During each stage, the main line and down legs were cycled. All quench effluent was neutralized and disposed safely on site; and the ends of the pipe were capped until the line was put into service.
Case Study: Chemical Application for a Fin Fan Air Cooler
A power plant’s air cooler system was not performing to standard. After further investigation, their fin fans were coated with organics from a nearby cat tail and cottonwood vegetation outside of the plant.
Eagle Services utilized their patent foam cleaning system that applied a low-pressure high-volume foam which attacked the organic coating on the fans, and after an hour of wait time was then rinsed off with a low pressure water system. The cleaning removed the foulant without damaging the integrity of the fans and the plant was back to running at full capacity.
